Level sensors are instruments that measure the level of liquid or bulk solids in tanks or containers. The primary function of these sensors is to provide accurate and reliable level measurement, which is essential for process control, inventory management, and safety. There are various types of level sensors available in the market, each with unique features and benefits. In this blog, we will discuss the different types of level sensors, their applications, and how to select the right sensor for your application.
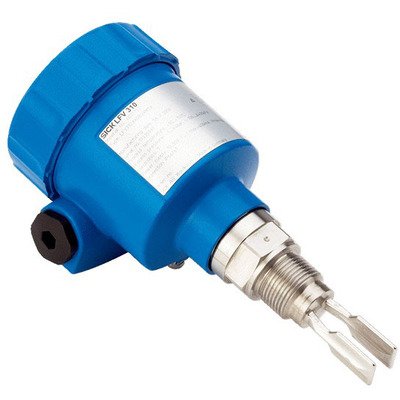
Types of Level Sensors:
Float Level Sensor:
A float level sensor consists of a float that moves up and down with the level of the liquid. The float is attached to a shaft that is connected to a switch. As the float moves up and down, it triggers the switch, sending a signal to the controller. Float level sensors are simple, reliable, and cost-effective. They are commonly used in small tanks or containers.
Capacitance Level Sensor:
Capacitance level sensors measure the change in capacitance between the sensor and the liquid or bulk solid. As the level of the liquid or bulk solid changes, the capacitance changes, which is detected by the sensor. Capacitance level sensors are ideal for detecting the level of conductive and non-conductive liquids, as well as bulk solids.
Ultrasonic Level Sensor:
Ultrasonic level sensors use high-frequency sound waves to measure the level of the liquid or bulk solid. The sensor sends out a sound wave, which bounces off the surface of the liquid or bulk solid and returns to the sensor. The time it takes for the sound wave to return is measured, and the level of the liquid or bulk solid is calculated. Ultrasonic level sensors are suitable for a wide range of liquids and bulk solids, and they can be used in tanks or containers of any size.
Optical Level Sensor:
Optical level sensors use infrared light to detect the level of liquid in a container. The sensor emits a beam of infrared light, which is reflected back to the sensor by the surface of the liquid. The level of the liquid is determined by the amount of light that is reflected back to the sensor. Optical level sensors are ideal for measuring the level of clear liquids such as water, oil, and chemicals.
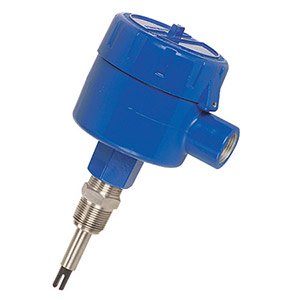
Applications of Level Sensors
Level sensors have a wide range of applications in various industries, such as oil and gas, chemical processing, food and beverage, pharmaceutical, and water and wastewater treatment. Here are some of the common applications of level sensors:
- Inventory Management: Level sensors are used to monitor the level of liquid or bulk solid in tanks and containers. This information is used to manage inventory levels, ensuring that there is enough product available for production or distribution.
- Process Control: Level sensors are used to control the flow of liquids and bulk solids in industrial processes. The sensors provide real-time information about the level of the product, allowing operators to adjust the flow rate to maintain consistent levels.
- Safety: Level sensors are used to monitor the level of hazardous materials in tanks and containers. If the level of the material exceeds the safe limit, the sensor can trigger an alarm, alerting operators to take appropriate action.
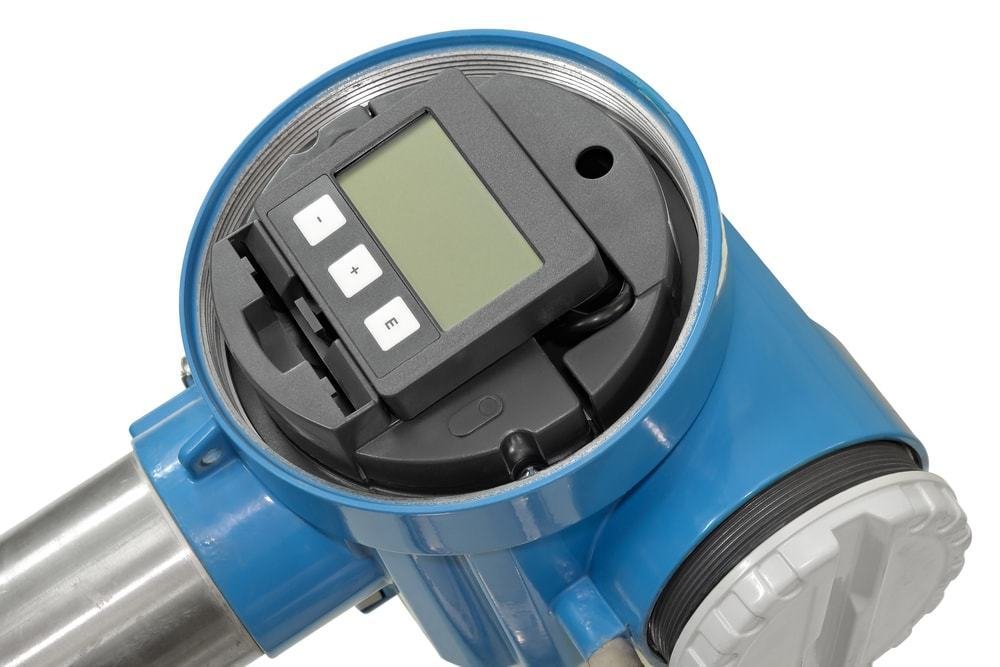
How to Select the Right Level Sensor
Selecting the right level sensor for your application requires careful consideration of several factors, such as the type of material being measured, the size and shape of the tank or container, the operating environment, and the accuracy and reliability required. Here are some tips to help you select the right level sensor:
- Material Compatibility: Make sure the level sensor is compatible with the material being measured. Some sensors are designed for specific materials, such as liquids or bulk solids, and may not work well with other materials.
- Consider the size and shape of the tank or container. Some level sensors are better suited for small tanks, while others can be used in large tanks or containers. Additionally, the shape of the tank or container can impact the performance of the level sensor. For example, a float level sensor may not work well in a tank with irregular shapes or sloping sides.
- Operating Environment: Consider the operating environment when selecting a level sensor. For example, if the sensor will be used in a corrosive or high-temperature environment, a sensor with a robust construction may be required.
- Accuracy and Reliability: Consider the required level of accuracy and reliability. Some sensors may have a higher degree of accuracy than others, and some may be more reliable in certain applications. It’s important to select a sensor that meets your specific needs.
- Cost: Consider the cost of the sensor. While it’s important to select a sensor that meets your requirements, it’s also important to consider the cost. Some sensors may be more expensive than others, and you may need to balance cost and performance when making your selection.
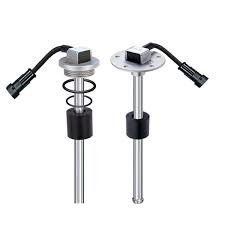
Conclusion
Level sensors are essential instruments for measuring the level of liquid or bulk solids in tanks and containers. There are various types of level sensors available, each with unique features and benefits. Selecting the right level sensor for your application requires careful consideration of several factors, such as the type of material being measured, the size and shape of the tank or container, the operating environment, and the required level of accuracy and reliability. By selecting the right level sensor, you can ensure accurate and reliable level measurement, which is essential for process control, inventory management, and safety.